OCTG Connection Development
The MHC team has the capabilities to create and document all phases of new specialized connection development. Our team consists of all veteran highly experienced specialist in the OCTG industry.
MHC has the experience and capabilities to help and assist document manufacturers with new specialized connections required in the ever changing oil and gas industry. All the way from inception to prototype manufacture to (in-house FEA and physical third party testing) to high production and then to down-hole running procedures. We are a One Stop Shop.
We are an engineering firm not a manufacturing facility. However we can advise prototype and licensee facilities.
MHC Specialties:
- Tubing Configurations
- Casing Configurations
- Specialized Drill Pipe Connections
- High End/High Torque Resistant Connections
New specialized connections are constantly needed as the drillers create new drilling techniques that are safe for our precious environment. These drilling techniques are constantly changing as the drilling practices develop better techniques in oil recovery and vigorously demand a safe environment.
Because the industry is discovering that “one connection fits all design” will not satisfy their requirements, the industry is leaning to a “fit for purpose” approach. This approach requires a specialized connection design configurations that focuses on the performance requirements that the driller needs to complete his well safely. This “Fit for Purpose” approach saves considerably capital in manufacturing. Also physical testing because the test is truncated focused only to required performance requirement(s).
The universal USA standard API 5C5 testing procedure “one connection fits all design “ forces the manufacture to create very costly and complicated super premium connections that normally does not suit the driller in his well design to be competitive in the market. Cost prohibitive.
The “Fit for Purpose “approach is still tested according to the USA standard API 5C5, but truncated to the performance requirements to the well it will be used. This approach is very successful because the manufacturer and the user work very closely together and become a team to successfully complete a project. Plus the capital to develop and test is greatly reduced plus the time to market is greatly reduced.
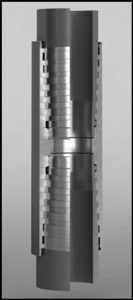
Over the past 35+ years, our team members have developed all kinds of different connection for the OCTG industry. Because of past NDA’s we are unable to publish past projects. However, feel free to contact us for more details about our past experiences.
Popular Connection Configurations:
Thomas L Blose was the chief engineer of R&D at that point of time and was assigned to investigate the possibility of a new high performance connection. It was actually created on a manual thread lathe. It was determined at that time the thread could not be created economically in production to compete in the market.
During the early 1970’s the Numerical Controlled Lathes started to be mass produced. Tom Blose believed that the NC Lathes could possibly unleash the economics of producing the new high performance connection. So Tom landed a job at a premiere OCTG connection company to develop this new technology and Patent the technology. He liked the name Wedge to describe the thread technology.
Wedge Vs. Non-Wedge Connections:
Tom started the R&D of this unique technology in the mid 1970’s. This included new machining techniques and quality control. Many prototypes and configurations were designed to verify its advantages over the present connections on the market.
The technology was put on the market in the early 1980’s, however very slow for acceptance because users did not like the idea of being guinea pigs. So basically the acceptance of the technology in the market was in the 1990’s after the technology was proven by many users. Looking forward now the technology is preferred by users over the conventional technology.
Tom’s technology that he used, was his theories produced from Armco Steel R&D. This included thread form geometry and metal to metal seal technology. He was known as the premiere in this technology and if was not for him, the technology would not exist today.
We at HMC are his pupils and practice the (Toms) Armco Steel Research.